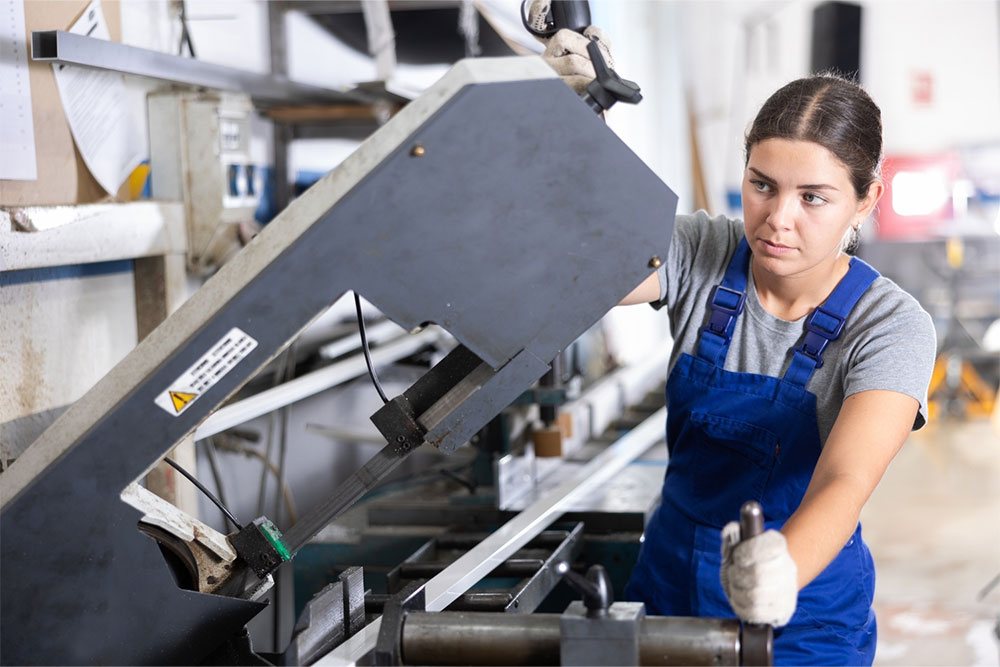
PVC extrusion machine – Types, functions, and uses
Polyvinyl chloride (PVC) is a synthetic plastic polymer known for its durability and flexibility. Since it’s quite cheap compared to other materials, it is widely used for making pipes, sheets, cables, and others. Extrusion is basically a process in manufacturing where a material, like raw plastic in this case, is melted and passed through a die to produce the desired pipe shape. The process of PVC extrusion is also colloquially called plastic extrusion.
Overview
Plastic extrusion technology can convey, mix, shear, and transform plastic into various products, like tubes, window frames, weather tripping, or wire insulation. The PVC materials are durable, easy to install, highly customizable, cost-effective, and also fire-resistant. Even with PVC, there are types like flexible PVC that are softer and easier to bend. It is used mainly for electrical wire insulation, and many residential and commercial builders use it for construction. Another category is rigid PVC, which is strong but lightweight and can be used for making large doors, decking pieces, etc., as well as in industries like automotive, construction, and even marine applications. One can enlist the services of different PVC extrusion companies to custom-make products for one’s project.
Types
There are two main types of plastic extrusion machines: single-screw and twin-screw. The single-screw extruders are reliable and straightforward, where a single rotating screw pushes the PVC material through the barrel and die system. The twin one, as the name suggests, uses two screws and mixes ingredients more uniformly. Here, the process is suitable for more complex formulations. There are also co-extrusion machines that work with PVC as well as other types of thermoplastic materials and create products with more aesthetic finish.
Features
1. Screw systems
The machines look relatively simple but have complex mechanisms at each step. Screws, for example, create the necessary energy to heat the material and prepare it for extrusion. They are placed in three different zones: the feeding zone and melting zone, where the material is fed, and the final zone, where a uniform temperature is maintained through different processes, including heating, fans, and cooling.
2. Temperature control system
The barrel of the extruder has temperature control mechanisms to avoid producing substandard products. Usually, the temperature decreases gradually from the front to the back before reaching the next stage.
3. Process of die
This is the part responsible for ensuring that the final product does not lose its shape. The die is the tool attached to the extrusion machine that shapes the molten PVC. After this, it is cooled into the profile, which is the actual shape or design. So, the material is extruded through the profile to obtain the desired final product. The die process takes little time and can produce high volumes or results, which helps shorten the overall manufacturing time.
4. Continuous profile
The PVC extrusion machine is capable of heating and melting raw materials like granules, pellets, flakes, and powders and makes long continuous products. After the die, the product is still soft and pliable. During the cooling process, where the product gets a water bath or is exposed to air cooling, the polymer hardens to form the final product. This process takes place immediately to ensure that it retains its shape.
5. Versatile
PVC extrusion machines are highly versatile and capable of creating products of varying sizes, shapes, thicknesses, colors, and textures. Some additives may be necessary to help change the original product’s properties, like making it more durable and fire resistant, but the overall process is quick and cost-effective.
Applications
1. Construction sector
PVC pipes made through extrusion are extensively used for drainage solutions, irrigation, and firefighting systems. The material is recyclable, safe, and durable, so these pipes have a minimal failure rate.
2. Window profiles
PVC is widely used for cladding, flooring, and wall covering, which are related to window profiles. These products do not require frequent painting and do not disintegrate easily, like in the case of iron. The PVC machine also provides insulation, thus lowering the energy expenditure. PVC windows and pellets are quite popular for their weather-resistant quality.
3. Floors and decking
PVC extruders are used in the flooring and decking of hospitals, sports institutions, kitchens, and even buildings. These floors are waterproof and can be customized to one’s preference, including color, shape, and size. They also provide UV resistance.
4. Electric cable industry
Since PVC is not affected by electric current, it is used extensively in making cables and conduits. The thermal efficiency of the PVC remains consistent and durable. When used properly, it rarely hardens or breaks and can withstand mild to extreme fluctuations in temperature.
- Previous Post
- Next Post